Glossary of Key Technology Terms for Supply Chain and Operations Professionals
If you’re confused by the acronym soup used in the operations and supply chain tech world, you’re not alone. It can be especially difficult to navigate device and platform overlaps or vendor claims when searching for new technology or solutions for your business.
Consult this list of operations supply chain technologies (listed in alphabetical order) to gain clarity. Learn about the standard definitions of these technologies, what is (or isn’t) typically solved-for with their implementation, and why solutions providers often sugarcoat half-baked capabilities for marketing purposes.
We hope you also see that, at GPX Intelligence, we are straight-shooters and are here to help you find solutions that make a real difference in your business. We’re here to help you shine a light on the unknown, yet critical details within your organization.
What is an Automated Guided Vehicle (AGV)?
- Abbreviation: AGV = Automated Guided Vehicle
- AGV Definition: An Automated Guided Vehicle (AGV) is a self-operating vehicle or robot used in industrial and commercial settings to transport materials and goods. AGVs are designed to follow predetermined paths or use navigation technologies like lasers, cameras, or magnets to autonomously move through warehouses, manufacturing facilities, or distribution centers.
- Industry applications: AGVs are an integral part of automation in industries like logistics, manufacturing, and e-commerce, offering precision and efficiency for repetitive tasks but requiring a structured environment for optimal operation.
- Typical features:
- Materials transport and handling | Transport raw materials, finished goods, or components between workstations, storage areas, or loading docks. May move pallets, rolls, racks, or bins efficiently.
- Order fulfillment and picking | Some AGVs are equipped to assist in picking and packing, often working in conjunction with warehouse management systems (WMS).
- Inventory management | Integrated with inventory systems, they can automatically retrieve or store items, updating inventory records in real time.
- Assembly line support | Deliver parts and components to assembly lines in just-in-time (JIT) manufacturing systems.
- Customizable operations | AGVs can be tailored to specific tasks, such as towing, lifting, or even robotic arm attachments for added functionality.
- Navigation and collision avoidance | Use sensors, lasers, cameras, or mapping software to detect obstacles and avoid collisions.
- 24/7 operation | Perform tasks continuously without requiring breaks, provided they have access to power or charging infrastructure.
- Does not typically include:
- Unstructured navigation | Traditional AGVs require predefined paths, such as magnetic strips, QR codes, or mapped routes, and cannot operate well in unstructured or unpredictable environments (unlike AMRs—Autonomous Mobile Robots).
- Complex problem solving | AGVs follow programmed tasks and lack the ability to make complex, real-time decisions beyond their navigation and task parameters.
- Manual intervention tasks | Tasks requiring human judgment, dexterity, or adaptation (e.g., custom packaging or quality control) are beyond AGVs’ capabilities.
- Vertical or complex movements | Standard AGVs typically don’t handle vertical tasks like retrieving items from high racks, unless equipped with specific lifting mechanisms.
- Dynamic pathfinding | Unlike AMRs, AGVs cannot dynamically reroute themselves in real time when faced with obstructions if their environment isn’t equipped with predefined alternate paths.
- Human collaboration | AGVs don’t inherently work alongside humans in the same way collaborative robots (cobots) do, as they are primarily built to work in more isolated or controlled spaces.
What is an Asset Maintenance Management Service (AMMS)?
- Abbreviation: AMMS = Asset Maintenance Management Services
- AAMS Definition: An Asset Maintenance Management Service (AMMS) is a platform or solution designed to help organizations efficiently monitor, maintain, and manage their physical assets, such as equipment, machinery, vehicles, or infrastructure. These services typically aim to maximize asset lifespan, minimize downtime, and optimize operational efficiency by streamlining maintenance processes and providing actionable insights into asset health.
- Industry applications: By focusing on what assets need to stay operational and efficient, these platforms address specific needs tied to upkeep and reliability, forming a critical part of operations in industries like manufacturing, logistics, construction, and utilities.
- Typical features:
- Asset tracking & inventory management | Keeping records of assets, their locations and their statuses. Usually, this involves integration with GPS or IoT tracking solutions for real-time updates.
- Preventative maintenance scheduling | Tools to schedule routine maintenance, based on time intervals or usage data. Solutions often include notifications and reminders for upcoming tasks.
- Predictive maintenance | Solutions use sensor data to detect potential failures before they occur. Often, this is also supported by robust analytics or prediction engines.
- Work order management | Creating, assigning, and tracking maintenance tasks and repairs. This is typically accessible on mobile devices for on-the-go updates.
- Maintenance records and compliance | Logs past maintenance activities for audits, ensuring compliance with industry regulations or safety standards.
- Spare parts inventory | Tracks and manages spare parts inventory to ensure availability when needed. Platforms may even automatically reorder parts when stock is low, based on settings.
- Reporting and analytics | Dashboards show asset performance, maintenance costs, and downtime. Additional tools may be included, like trend identification and maintenance schedule optimization suggestions.
- Integration | Companies often look for these platforms to integrate with ERP systems, accounting platforms, or IoT devices. Or, at the very least, offer an open API for custom integrations.
- Does not typically include:
- Full asset lifecycle management | While maintenance platforms focus on the upkeep phase, lifecycle management includes procurement, asset financing, and eventual decommissioning or resale.
- Financial management or accounting tools | These services usually don’t handle detailed accounting, invoicing, or tax calculations beyond basic cost tracking for maintenance activities.
- Manufacturing process management | They don’t manage production schedules, workflows, or manufacturing operations directly.
- Project management tools | Broader project management capabilities (e.g., team collaboration on non-maintenance tasks) are often outside the scope.
- Human resources management | They don’t typically track employee performance, payroll, or HR-related data, though they may store technician certifications and training records.
- Facility management | While overlapping in some cases, facility management platforms focus on the building itself rather than specific machinery or operational assets.
- Non-Asset-Specific services | General task management, communication tools, or CRM functionalities are usually not part of the platform unless tangentially integrated.
What is an Automated Mobile Robot (AMR)?
- Abbreviation: AMR = Autonomous Mobile Robot
- AMR Definition: An Autonomous Mobile Robot (AMR) is a self-navigating robotic system designed to operate in dynamic and unstructured environments. Unlike Automated Guided Vehicles (AGVs), which rely on predefined paths, AMRs use advanced sensors, cameras, and AI-driven software to make real-time decisions about navigation and task execution.
- Industry applications: AMRs are increasingly adopted in industries like logistics, e-commerce, manufacturing, and healthcare due to their flexibility, adaptability, and ability to operate in complex, real-time environments without needing static infrastructure.
- Typical features:
- Dynamic navigation | Use LiDAR, cameras, or 3D mapping to understand and adapt to their surroundings, rerouting around obstacles or finding the most efficient path.
- Material transport and handling | Move goods, parts, or tools within warehouses, manufacturing facilities, or retail environments without predefined routes.
- Order picking and fulfillment | Some AMRs assist in picking items for orders by guiding workers to the right locations or retrieving items themselves.
- Collaborative tasks | Work alongside humans, enhancing efficiency in warehouses or production lines by performing repetitive transport tasks while humans focus on more complex responsibilities.
- Multi-tasking | Handle multiple assignments simultaneously, such as delivering goods to multiple locations in one trip, based on priority or efficiency.
- Autonomous learning | Continuously learn and improve route optimization and task performance by analyzing operational data and patterns.
- Safety and obstacle avoidance | Equipped with safety protocols, AMRs can detect people, objects, or other robots and stop or reroute to prevent collisions.
- Does not typically include:
- Structured path dependence | Unlike AGVs, AMRs are not constrained to predefined routes or infrastructure like magnetic strips or QR codes. However, this means they may not always be the best choice for highly predictable, static environments.
- Heavy load handling | AMRs are often designed for light-to-medium loads. They typically cannot handle extremely heavy items unless specifically designed for such purposes (e.g., forklifts or towbot AMRs).
- Complex dexterity | Standard AMRs lack the fine motor skills of robotic arms or human workers, making them less suited for tasks like assembly or precision adjustments.
- Outdoor navigation | AMRs are primarily used indoors; most models are not equipped for uneven terrain, weather conditions, or external environments.
- Long distance transport | Unlike trucks or drones, AMRs are meant for short-distance tasks within facilities, not for large-scale transport.
- Standalone intelligence | While advanced, AMRs rely on integration with Warehouse Management Systems (WMS) or Manufacturing Execution Systems (MES) for coordination and optimization across operations.
What is an Asset Performance Management (APM) System?
- Abbreviation: APM = Asset Performance Management (System)
- APM Definition: An Asset Performance Management (APM) system is a software platform that uses data, analytics, and predictive insights to monitor, optimize, and improve the performance and reliability of physical assets. APM systems aim to reduce downtime, extend asset lifespans, and enhance operational efficiency by integrating maintenance strategies with advanced analytics.
- Industry applications: APM systems are especially valuable in industries with high-value, critical assets, such as energy, utilities, manufacturing, and transportation. By focusing on performance, reliability, and predictive maintenance, APM helps organizations maximize asset ROI while reducing risks and inefficiencies.
- Typical features:
- Asset monitoring and diagnostics | Real-time tracking of asset performance metrics like temperature, pressure, vibration, or operational speed. May also detect and alert on anomalies or deviations from normal operating conditions.
- Predictive maintenance | Using machine learning and historical data to predict when an asset might fail, enabling preemptive maintenance to minimize downtime.
- Reliability analysis | Tools to assess and improve asset reliability, including root cause analysis (RCA) to identify recurring issues.
- Performance optimization | Analytics to fine-tune asset operations for maximum efficiency, balancing productivity with wear and tear.
- Risk assessment and management | Evaluating the likelihood of asset failures and their potential impact on operations or safety, and providing recommendations to mitigate risks.
- Integration with IoT and sensors | Compatibility with sensors and devices that collect real-time asset data, enabling continuous monitoring.
- Maintenance planning | Tools to plan and schedule maintenance activities based on asset condition rather than fixed schedules (condition-based maintenance).
- Data visualization and reporting | Dashboards that present performance, reliability, and maintenance metrics in user-friendly formats.
- Cost analysis and ROI tracking | Measuring the financial impact of maintenance strategies, downtime reduction, and asset efficiency improvements.
- Integration capabilities | Seamless integration with Enterprise Asset Management (EAM), Enterprise Resource Planning (ERP), and other systems for comprehensive data sharing.
- Does not typically include:
- Asset lifecycle management | APM focuses on operational and maintenance phases; it doesn’t typically cover procurement, disposal, or financial management of assets.
- Facility management |While there may be overlap in monitoring building systems (e.g., HVAC), APM is not a general facility management tool.
- Manual maintenance execution | APM provides insights and planning tools but doesn’t execute maintenance tasks—this requires technicians and related systems.
- Standalone IoT platforms | Although APM integrates with IoT devices, it’s not a substitute for platforms that manage IoT ecosystems broadly.
- Project management | Broader project management tasks, like construction or IT development, are beyond the scope of APM.
- Inventory or supply chain management | While APM can track parts needed for maintenance, it does not manage supply chains or procurement workflows comprehensively.
What is an Building Information Monitoring (BIM) System?
- Abbreviation: BIM = Building Information Monitoring (System)
- BIM Definition: A Building Information Monitoring (BIM) system is a digital platform designed to manage, monitor, and analyze information about a building’s physical and functional characteristics throughout its lifecycle. BIM systems centralize data and provide a real-time view of a building’s performance, supporting operations, maintenance, and long-term planning. These systems often use IoT devices, sensors, and integrations to collect and interpret data.
- Industry applications: BIM systems are invaluable for building owners, facility managers, and operations teams looking to ensure optimal performance, sustainability, and comfort in modern buildings. By integrating advanced monitoring and automation, they support smarter, more efficient building management.
- Typical features:
- Building performance monitoring | Real-time tracking of building systems like HVAC, lighting, water, and energy usage. Typically provides alerts for anomalies or inefficiencies.
- IoT integration | Connectivity with sensors and IoT devices to capture data on occupancy, temperature, air quality, humidity, and more.
- Space utilization analysis | Tools to track and analyze how building spaces are being used, such as occupancy rates, flow of people, and density.
- Energy management | Monitoring energy consumption and providing insights into optimizing energy efficiency. Often integrates with renewable energy systems and sustainability initiatives.
- Predictive maintenance | Identifying maintenance needs before issues arise based on sensor data and performance analytics.
- Centralized data management | A shared digital repository for information about the building’s design, construction, systems, and operational history.
- Asset and equipment tracking | Monitoring the status, location, and usage of critical equipment within the building.
- Building automation system (BAS) integration | Connecting with BAS for automated control of systems like lighting, heating, cooling, and security.
- Dashboards and reporting | Visualizations of building performance metrics and customizable reports on areas such as energy use, maintenance schedules, and occupant comfort.
- Compliance and regulatory tracking | Ensuring adherence to safety, environmental, and building code regulations through ongoing monitoring.
- Does not typically include:
- Architectural design and planning | BIM systems manage and monitor buildings post-construction; they do not perform the 3D modeling or design work typical of Building Information Modeling (same acronym but different focus).
- Construction project management | BIM systems monitor completed buildings, not the processes or workflows during construction.
- Facility cleaning services | While they might track cleanliness metrics (e.g., air quality), they don’t manage cleaning schedules or teams.
- Tenant or lease management | Although space utilization is a core feature, BIM systems don’t typically handle lease agreements or tenant management.
- Broad enterprise management | BIM is specialized for building operations and monitoring, not for broader enterprise resource management.
- Standalone security systems | While BIM can integrate with security systems, it doesn’t replace tools designed for access control, video surveillance, or cybersecurity.
- Detailed employee management | While occupancy and space tracking are included, employee management (e.g., HR functions) is not.
- Notable differences in BIM vs BAM vs BAS:
- We’ve included a detailed breakdown of BIMs in our glossary (and not BMS or BAS tools), as BIMs are much more aligned to GPX’s focus on warehousing, manufacturing, and supply chain. While important, the other platforms noted here are more focused on direct control of building infrastructure.
- Building Information Monitoring (BIM): A platform that tracks and analyzes real-time performance data of a building’s systems and assets, ensuring operational efficiency and sustainability throughout its lifecycle. Its primary use is to provide insights into energy usage, maintenance needs, space utilization, and overall building performance. BIMs are focused on real-time monitoring and long-term efficiency, integrating IoT data for analytics and reporting. BIMs are mostly leveraged by facility managers, sustainability teams, and operations analysts.
- Building Management Systems (BMS): A centralized system for monitoring and controlling a building’s mechanical, electrical, and plumbing (MEP) systems, such as HVAC, lighting, and energy management. BMS’ allow operators to oversee and manage key infrastructure like HVAC, lighting, fire systems, and elevators. The scope of these platforms is mainly on system-wide monitoring and manual control to maintain operational consistency. BMS’ are mostly leveraged by building operators and maintenance teams.
- Building Automation Systems (BAS): A system that automates the control of building systems like HVAC, lighting, and security to enhance energy efficiency, comfort, and operational reliability. BAS’ automate tasks like adjusting lighting based on occupancy or optimizing HVAC settings based on temperature sensors. The scope of these platforms is typically limited to managing energy efficiency. BAS tools are mostly leveraged by facility managers and energy management teams.
What is a Computerized Maintenance Management System (CMMS)?
- Acronym: CMMS = Computerized Maintenance Management System
- CMMS Definition: A Computerized Maintenance Management System (CMMS) is a software platform designed to streamline and automate maintenance operations for physical assets, such as equipment, machinery, vehicles, and facilities. The system centralizes maintenance-related data, providing tools to schedule, track, and document maintenance activities to improve efficiency, reduce downtime, and extend asset lifespans.
- Industry applications: CMMS platforms are ideal for industries like manufacturing, logistics, utilities, healthcare, and property management, where efficient asset maintenance is critical to operations. By automating and organizing maintenance activities, CMMS helps organizations reduce costs, minimize downtime, and extend the life of their assets.
- Typical features:
- Work order management | Tools to create, assign, prioritize, and track maintenance tasks, plus updates and notifications for task progress and completion.
- Preventative maintenance scheduling | Automated scheduling of routine maintenance based on time, usage, or other parameters to prevent breakdowns.
- Asset management | A central repository of asset information, including location, condition, maintenance history, and warranties, as well as tagging and tracking of equipment and machinery.
- Inventory and spare parts management | Monitoring stock levels of spare parts and consumables to ensure availability. Often, this includes alerts functionality for low inventory or automated reordering.
- Maintenance logs and history | Detailed records of all maintenance activities, including repairs, inspections, and upgrades.
- Reporting and analytics | Dashboards and reports on maintenance costs, downtime, asset performance, and technician efficiency. May also identify trends to improve maintenance plans.
- Compliance and safety tracking | Helps ensure adherence to safety standards, regulatory requirements, and inspection schedules.
- Integration with IoT and sensors | Integration with IoT devices to collect real-time data on asset performance and trigger maintenance alerts.
- User roles and permissions | Assigning roles and access levels to team members based on responsibilities (e.g., managers vs. technicians).
- Does not typically include:
- Broad enterprise asset management (EAM) | CMMS focuses on maintenance management, while EAM systems provide broader functionality, including asset lifecycle and financial management.
- Advanced predictive analytics | While some CMMS platforms may integrate predictive maintenance tools, full-scale predictive analytics is typically handled by specialized Asset Performance Management (APM) systems.
- Project management tools | CMMS does not manage broader projects like facility construction or asset acquisition.
- Accounting or financial management | CMMS tracks costs related to maintenance but does not manage budgets, invoicing, or other financial processes.
- Facility-wide monitoring (BAM or BAS) | CMMS focuses on individual assets, not whole-building system monitoring like Building Management Systems (BMS) or Building Automation Systems (BAS).
- Standalone IoT platforms | While CMMS may integrate with IoT for real-time asset data, it doesn’t function as a standalone IoT ecosystem manager.
What is an Enterprise Asset Management (EAM) platform?
- Abbreviation: EAM = Enterprise Asset Management
- EAM Definition: An Enterprise Asset Management (EAM) platform is a comprehensive software solution designed to help organizations manage the entire lifecycle of their physical assets, from acquisition and deployment to maintenance and disposal. EAM platforms are used to optimize asset performance, reduce costs, and ensure compliance while supporting strategic decision-making.
- Industry applications: EAMs are widely used in industries with high-value, critical assets, such as manufacturing, energy and utilities, transportation and logistics, healthcare, government and public infrastructure.
- Typical features:
- Asset lifecycle management | Tracks assets through their entire lifecycle, including procurement, usage, maintenance, upgrades, and retirement. This provides visibility into asset ownership, location, and value.
- Maintenance management | Tools for preventive, predictive, and corrective maintenance planning and execution, and often integrates with work order systems to assign and track maintenance tasks.
- Inventory and spare parts management |Tracks inventory levels of parts and consumables, ensuring timely reordering to avoid downtime.
- Performance monitoring and reporting | Monitors asset performance metrics through dashboards and custom reports to identify inefficiencies and improve operations. Reports usually include tracking of costs, usage, and reliability.
- Compliance and risk management | Ensures adherence to industry standards, safety protocols, and regulatory requirements.
- Capital planning and budgeting | Supports long-term planning for capital investments and provides tools for forecasting asset costs, replacements, and upgrades.
- Integration with IoT and sensors | Collects real-time data from IoT-enabled assets for condition monitoring and predictive maintenance.
- Integration with other systems | Connects with ERP, CMMS, financial, and supply chain systems for a unified view of asset-related operations.
- Does not typically include:
- Facility management | While EAM platforms manage physical assets, they don’t typically focus on facility services like janitorial scheduling or space planning.
- Building automation or management | EAM systems do not control building systems like HVAC or lighting directly, though they may monitor their performance as assets.
- Project management tools | Broader project management (e.g., construction planning or IT development) is beyond EAM’s scope, though related tasks (e.g., asset deployment) may be included.
- Supply chain management | EAM tracks inventory and procurement for maintenance purposes but doesn’t handle broader supply chain logistics.
- Employee management | EAM platforms might track technician certifications but do not handle payroll, HR functions, or general employee data.
- Broader financial management | While EAM includes cost tracking and budgeting for assets, it doesn’t manage broader accounting processes like payroll, invoicing, or taxes.
What is an Electronic Logging Device (ELD)?
- Abbreviation: ELD = Electronic Logging Device
- ELD Definition: An Electronic Logging Device (ELD) is a device used in the transportation and logistics industry to automatically record a commercial vehicle driver’s driving hours, ensuring compliance with Hours of Service (HOS) regulations mandated by government agencies such as the Federal Motor Carrier Safety Administration (FMCSA) in the U.S. ELDs replace traditional paper logbooks with digital, tamper-proof systems.
- Industry applications: ELDs are focused tools for regulatory compliance in the transportation industry, providing a foundation for accurate HOS tracking while integrating with broader fleet management systems for enhanced capabilities.
- Typical features:
- Hours of service (HOS) tracking | Automatically records driving time, on-duty time, and rest periods in compliance with HOS rules.
- Vehicle data integration | Connects to the vehicle’s engine to capture real-time data such as engine hours, vehicle movement, and mileage.
- Driver log management | Allows drivers to view and edit their logs (with restrictions to maintain compliance) and certify the accuracy of their records.
- Compliance reporting | Generates logs and reports for inspections, audits, or enforcement officers in standard formats (e.g., PDF or electronic data transfer).
- Driver alerts | Provides notifications for upcoming breaks, maximum driving limits, or violations to help drivers stay compliant.
- GPS tracking | Records the vehicle’s location at regular intervals for accurate trip and HOS documentation.
- User interface | Touchscreen or app-based interfaces for drivers to interact with the device and access logs.
- Data storage and transfer | Stores log data and enables transfer to enforcement officials via USB, Bluetooth, or email, as required by regulations.
- Tamper prevention | Includes safeguards to prevent unauthorized changes to logs or tampering with device functionality.
- Integration with fleet management systems | Often integrates with broader fleet management platforms for tracking vehicle performance, compliance, and dispatch.
- Does not typically include:
- Advanced fleet management features | ELDs are primarily compliance tools; they do not inherently provide advanced route optimization, dispatching, or cargo tracking unless integrated with a fleet management system.
- Maintenance management | While some ELDs may collect engine data, they don’t typically provide tools for scheduling or managing vehicle maintenance tasks.
- Driver behavior analytics | Basic ELDs may not analyze driver performance metrics like harsh braking, idling, or fuel efficiency, though these features are available in more comprehensive telematics systems.
- Cargo monitoring | ELDs do not track cargo-specific data such as temperature or weight, which requires separate IoT sensors or systems.
What is an Enterprise Resource Planning (ERP) System?
- Abbreviation: ERP = Enterprise Resource Planning (System)
- ERP Definition: An Enterprise Resource Planning (ERP) system is a comprehensive software platform used by organizations to manage and integrate core business processes across departments in a centralized system. ERP systems streamline operations, provide real-time data insights, and improve collaboration by consolidating activities like finance, supply chain, human resources, manufacturing, and customer relationship management.
- Industry applications: An ERP system is a backbone software platform for integrating and managing core business functions, offering operational efficiency and real-time insights while relying on specialized systems for niche tasks or deeper capabilities. This is especially useful within the manufacturing, retail, eCommerce, healthcare, construction, logistics and transportation, and goverment sectors.
- Typical features:
- Financial management | Offers tools for managing accounting, budgeting, invoicing, and financial reporting as well as tax compliance and cash flow tracking.
- Human resources management (HRM) | Handles payroll, benefits, recruitment, employee records, and performance tracking.
- Supply chain management (SCM) | Tracks procurement, inventory, vendor relationships, and logistics. This ensures efficient management of raw materials, production, and delivery.
- Manufacturing and production planning | Provides tools for managing production schedules, work orders, and shop floor operations. This often includes capabilities for quality control and resource planning.
- Inventory and warehouse management | Tracks inventory levels, stock movement, and warehousing operations, in addition to supporting demand forecasting and replenishment planning.
- Customer relationship management (CRM) | Logs customer interactions, sales pipelines, and marketing campaigns and may include tools for tracking leads, opportunities, and customer support.
- Data and analytics | Centralized dashboards for monitoring performance metrics across departments. Often includes advanced reporting and forecasting tools for strategic decision-making.
- Integration and scalability | Connects with external systems (e.g., IoT, EDI, third-party applications). Companies’ need for these integrations usually scales with their growth.
- Project management | Tracks relevant project timelines, budgets, and resource allocation.
- Compliance and risk management | Ensures adherence to industry-specific regulations and standards, as well as providing audit trails and security features for sensitive data.
- Does not typically include:
- Tools specialized industries | Offer broad functionality but may lack depth in specialized areas (e.g., niche manufacturing processes or advanced scientific data analysis).
- IoT and real-time asset monitoring | May integrate with IoT platforms but do not typically perform real-time asset tracking or monitoring on their own.
- Standalone maintenance management | While some ERP systems have basic maintenance tracking, full-featured CMMS or EAM platforms provide more robust solutions for asset maintenance.
- Advanced marketing tools | Might include basic CRM features but don’t typically handle advanced marketing automation, content management, or SEO.
- Highly customizable applications | Systems often require standardization and may lack the flexibility of custom-built software tailored to specific workflows.
- Physical infrastructure management | ERP’s do not manage facilities, building automation, or environmental controls.
- Consumer-focused features | Designed for business operations, not consumer-facing applications like e-commerce platforms or retail POS systems (though integrations are possible).
What is a Global Positioning System (GPS) Device?
- Abbreviation: GPS = Global Positioning System
- GPS Definition: A Global Positioning System (GPS) device is a tool that uses satellite signals to determine and track its precise location on Earth. These devices are widely used for navigation, tracking, and geolocation in various industries, including transportation, logistics, agriculture, and personal use.
- Industry applications: By focusing on geolocation, navigation, and basic tracking, GPS devices serve as foundational tools for location-based services. Their functionality is often enhanced by integration with specialized platforms or complementary technologies for advanced applications.
- Typical features:
- Location tracking | Determines exact geographic coordinates (latitude and longitude) using signals from GPS satellites, providing real-time or historical location data.
- Time synchronization | Provides accurate time data synchronized with atomic clocks via satellite signals.
- Battery or power source | Operates on rechargeable batteries, vehicle power supplies, or solar charging, depending on the model.
- Connectivity | May include cellular, Wi-Fi, or Bluetooth capabilities to upload data or enable communication with other devices.
- Does not typically include:
- Independent communication features | Basic GPS devices don’t allow direct communication like calls or messaging unless paired with a communication-enabled system.
- Indoor location accuracy | Standard GPS struggles to provide precise location data indoors or in areas with weak satellite signals, such as tunnels or urban canyons. However, GPX Intelligence offers solutions that leverage both GPS and BLE, punching through prior indoor location barriers.
- Custom applications | Basic GPS devices are limited to navigation and tracking functions and don’t support specialized applications unless integrated.
- Non-navigation tasks | They don’t manage tasks like route optimization, maintenance planning, or logistics scheduling unless part of a broader system. GPX Intelligence provides a broader system that allows for improved device functionality.
What is IoT or IIoT (Internet of Things)?
- Abbreviation: IoT = Internet of Things, IIOT = Industrial Internet of Things
- IoT Definition: The Internet of Things (IoT) refers to the network of physical objects—”things”—embedded with sensors, software, and other technologies that enable them to connect to the internet and exchange data with other devices and systems. IoT allows these objects to collect, share, and analyze data, enhancing automation, efficiency, and decision-making across various industries.
- IIoT Definition: The Industrial Internet of Things (IIoT) refers to the use of interconnected sensors, devices, and machines within industrial environments to collect, analyze, and share data. IIoT enables automation, predictive maintenance, and enhanced operational efficiency, with applications in manufacturing, energy, logistics, healthcare, and other industrial sectors. It is a subset of the broader Internet of Things (IoT), specifically tailored for industrial use cases.
- Industry applications: IoT enables the seamless connection and communication of physical objects through the internet, transforming how devices operate, collect data, and interact. While IoT focuses on connectivity and data exchange, it doesn’t encompass standalone devices, human communication tools, or unrelated IT systems, emphasizing its role as the backbone of connected ecosystems in industries like healthcare, agriculture, manufacturing, and smart cities. IIoT encompasses industrial, agricultural, and commercial uses that go beyond personal devices.
- Typical features:
- Category of sensors and actuators | IoT/IIoT represents a category of hardware devices embedded with sensors to measure temperature, humidity, pressure, motion, location, and more. Actuators to enable actions like turning on/off equipment or adjusting settings based on data.
- Connectivity | Uses Wi-Fi, Bluetooth, cellular, Zigbee, LoRa, or satellite communication to share data with other devices or cloud systems.
- Edge devices and gateways | Localized devices that process and filter data before sending it to centralized systems or cloud platforms.
- Cloud storage and processing | Data collected by IoT devices is stored and analyzed in the cloud for scalability and accessibility.
- Real-time data collection | Continuous or near-real-time data collection for monitoring and immediate responses to changes in the environment or system.
- Industrial Automation | Automation of manufacturing, logistics, or operational processes, often using robotics, AI, or programmable logic controllers (PLCs).
- Digital twins | Virtual representations of physical assets that simulate performance and help in monitoring, diagnosing issues, and optimizing processes.
- Data analytics and insights | Tools to process and analyze IoT data for actionable insights, trends, and predictive modeling.
- Remote monitoring and control | Enables users to monitor and manage devices or systems remotely via apps or dashboards.
- Scalability | IoT networks can expand to include more devices, supporting growth in systems like smart cities or industrial operations.
- Does not typically include:
- Standalone devices without connectivity | Devices that don’t communicate with other systems or the internet, such as traditional thermostats or non-smart appliances, are not IoT.
- A single technology | IoT is an ecosystem of technologies (sensors, connectivity, analytics) rather than a single product or platform.
- Comprehensive enterprise software | IoT itself doesn’t provide enterprise-level project management, CRM, or ERP functionality unless integrated with such systems.
- Limitations to physical devices | IoT includes virtual platforms and cloud infrastructure as essential components, not just the devices themselves.
- Automatic integration with enterprise systems | It is up to the individual IoT provider to link with ERP, MES (Manufacturing Execution Systems), or EAM platforms for holistic management of all industrial operations.
What is an Inventory Management System (IMS)?
- Abbreviation: IMS = Inventory Management System
- IMS Definition: An Inventory Management System (IMS) is a platform or solution designed to track, manage, and optimize inventory levels, ensuring that businesses maintain the right stock at the right locations to meet demand while minimizing carrying costs. IMS platforms streamline inventory operations, improve accuracy, and enable data-driven decision-making.
- Industry applications: An IMS provides businesses with tools to track and optimize stock levels, ensuring operational efficiency and reducing costs. It focuses on managing inventory processes but requires integration with other platforms like ERP or CRM systems to address broader business functions. By improving accuracy and visibility, IMS solutions play a vital role in supply chain and operational success.
- Typical features:
- Inventory tracking | Monitors goods in real time across multiple locations, tracking movements like receiving, storing, and shipping.
- Barcode,RFID, networked GPS/BLE integration | Supports technologies to quickly and accurately update inventory data and enables automated updates when items are moved.
- Stock alerts and reordering | Sends notifications for low stock levels or overstocked items and automates purchase orders to suppliers based on predefined thresholds.
- Warehouse management | Includes tools for organizing stock within warehouses, such as bin locations and slotting. They may also optimize picking, packing, and shipping workflows.
- Reporting and analytics | Provides insights into inventory turnover, stock valuation, and demand forecasting. IMS’ typically generate detailed reports on inventory performance and trends.
- Integrations with other systems | Links with ERP, CRM, or e-commerce platforms to provide a unified view of inventory and sales.
- Cost tracking | Tracks the cost of goods sold (COGS) and carrying costs for inventory – also helps calculate profit margins and optimize procurement strategies.
- Multi-location support | Manages inventory across multiple warehouses, stores, or distribution centers and stock at each location.
- Demand forecasting | Predicts future inventory needs based on historical data and trends.
- Does not typically include:
- Production management | This system focuses on inventory; it doesn’t handle manufacturing processes or workflows directly, which are managed by MES (Manufacturing Execution Systems).
- Supply chain management | While IMS tracks inventory, broader supply chain functions like logistics optimization and vendor relationship management are typically outside its scope.
- Accounting and financial management | IMS may track inventory costs but doesn’t handle broader financial tasks like payroll, tax calculations, or financial reporting.
- Customer relationship management (CRM) | IMS doesn’t manage customer interactions or sales pipelines, though it can integrate with CRM systems for sales data.
- Facility management | IMS focuses on inventory and warehouse optimization, not facility maintenance or utilities management.
What is LoRaWAN? What is LPWAN?
- Abbreviation: LoRaWAN/LPWAN = Low Power Wide Area Networking
- LoRaWAN Definition: (Note the definition for WAN, below to understand the “WAN” portion of this acronym.) A LoRaWAN (Long Range Wide Area Network) is a communication protocol built on LPWAN (Low Power Wide Area Network) technology, designed for connecting low-power IoT devices over long distances with minimal energy consumption.
- LPWAN Definition: LPWAN is short for Low Power Wide Area Network and is the broader category of wireless networks that includes LoRaWAN, as well as other technologies like NB-IoT and Sigfox. These networks are optimized for transmitting small amounts of data over long ranges, making them ideal for IoT applications.
- Industry applications: LoRaWAN and LPWAN are low-power, long-range wireless technologies designed to connect IoT devices for applications requiring minimal energy use and small data transmission. They excel in remote monitoring and large-scale deployments but are unsuitable for high-bandwidth, low-latency, or real-time applications. These technologies are key enablers of smart cities, agriculture, and industrial IoT.
- Typical features:
- Low power consumption | Devices can operate for years on small batteries due to the energy efficiency of LoRaWAN and LPWAN protocols.
- Long-range connectivity | Supports communication over several kilometers in rural areas and up to a few kilometers in urban environments, depending on obstacles and network configuration.
- Low bandwidth data transmission | Designed to send small packets of data, such as sensor readings, rather than high-bandwidth content like video or large files.
- Device-to-gateway communication | IoT devices communicate with gateways, which relay data to central servers or cloud platforms for processing.
- One-to-many communication | Uses a star network architecture, where end devices communicate with one or more central gateways.
- Unlicensed frequency bands | Operates on unlicensed spectrum (e.g., ISM bands such as 868 MHz in Europe or 915 MHz in the U.S.), reducing operational costs.
- Bi-directional communication | Enables both uplink (device-to-server) and downlink (server-to-device) communication for applications like firmware updates or commands.
- Cloud integration | Data from gateways is often routed to cloud platforms for storage, analysis, and visualization.
- Does not typically include:
- Low-latency networks | LPWANs have higher latency compared to technologies like Wi-Fi or cellular networks, making them less ideal for time-sensitive applications.
- Short-range wireless technologies | Unlike Bluetooth or Wi-Fi, LoRaWAN and LPWAN are designed for long-range communication and are not used for close-proximity device connections.
- Device localization without GPS | While LPWAN networks can estimate device location using signal strength and triangulation, they do not inherently provide GPS-level accuracy.
- Universal connectivity | LPWANs are specialized for IoT and don’t replace cellular networks for voice or general internet connectivity.
- Heavy data processing | LPWANs don’t process data directly but serve as communication channels for transmitting data to external systems.
- Real-time control | Due to latency and low bandwidth, LPWAN is not suited for applications requiring real-time responses.
- Proprietary cellular networks | While LPWANs operate on unlicensed bands, some competing technologies like NB-IoT run on licensed cellular bands.
What is Near-Field Communication (NFC)?
- Abreviation: NFC = Near-Field Communication
- NFC Definition: Near-Field Communication (NFC) is a short-range wireless communication technology that enables devices to exchange data when they are within close proximity, typically less than 4 centimeters. NFC is widely used for secure transactions, device pairing, and information sharing, leveraging radio-frequency identification (RFID) technology standards.
- Industry applications: NFC is a secure, short-range communication technology ideal for applications like contactless payments, quick device pairing, and data sharing via simple taps. While NFC excels in user convenience and security for small-scale interactions, it is unsuitable for long-range, high-speed, or continuous data exchanges, distinguishing it from other wireless technologies like Bluetooth or Wi-Fi.
- Typical features:
- Short-range communication | Operates at very close ranges (typically 4 cm or less) to enhance security and prevent interference from other devices.
- Bi-directional communication | Allows devices to communicate bidirectionally for data exchange, such as between a smartphone and a terminal.
- Contactless secure communication | Powers payment systems like Apple Pay, Google Pay, and contactless credit cards by transmitting payment credentials securely. Security is created from encryption and short-range transmission to ensure that data exchanges are protected against interception.
- Device pairing | Simplifies the pairing process for Bluetooth devices or Wi-Fi networks, allowing quick and seamless connectivity.
- Data sharing | Enables the transfer of small amounts of data, such as contact information, URLs, or authentication credentials, with a simple tap.
- Physical device | Passive NFC-enabled devices (tags) can store data like product details or URLs and transmit it to active NFC readers (e.g., smartphones). Passive NFC tags draw power from the electromagnetic field of the NFC reader, making them energy-efficient.
- Interoperability | Operates on globally recognized standards (e.g., ISO/IEC 14443, FeliCa), ensuring compatibility across devices and systems.
- Does not typically include:
- Long-range communication | NFC only works over very short distances; it’s not suitable for applications requiring communication beyond a few centimeters.
- High-speed data transfer | Passive NFC tags don’t require a power source, but active NFC devices (e.g., smartphones) do.
- Continuous data streaming | NFC cannot handle continuous or real-time data exchange due to its low data rate and short-range limitations.
- Multi-device connectivity | NFC facilitates one-to-one communication, not one-to-many connections or mesh networking.
- IIoT | While NFC has applications in retail and consumer IoT, it is not designed for large-scale industrial IoT environments requiring long-distance communication.
- Replacement for RFID | NFC is based on RFID technology but operates at shorter ranges and offers additional capabilities like two-way communication.
What is a Quality Management System (QMS)?
- Abbreviation: QMS = Quality Management System
- QMS Definition: A Quality Management System (QMS) is a formalized framework of policies, processes, and procedures designed to ensure that an organization’s products or services consistently meet customer requirements and comply with industry standards. QMS is often implemented to improve operational efficiency, enhance customer satisfaction, and drive continuous improvement.
- Industry applications: A QMS is a structured framework for ensuring consistent quality in products or services, focusing on compliance, continuous improvement, and customer satisfaction. While QMS integrates into operations to manage quality-related activities, it doesn’t handle broader tasks like production scheduling, project management, or general customer relations. It is especially vital in regulated industries such as manufacturing, healthcare, and aerospace.
- Typical features:
- Document control | Centralized management of quality-related documents such as policies, procedures, and work instructions. Ensures version control, accessibility, and regulatory compliance.
- Process management | Standardizes workflows to maintain consistency and reduce variability in processes and includes tools for process mapping and performance monitoring.
- Compliance management | Ensures adherence to industry standards, regulations, and certifications (e.g., ISO 9001, FDA, GMP).
- CAPA/Corrective and Preventive Actions | Identifies, tracks, and resolves non-conformities in processes or products and helps implement preventive measures to avoid recurrence of issues.
- Auditing | Facilitates internal and external audits, including scheduling, tracking findings, and ensuring follow-up actions.
- Supplier and vendor management | Monitors supplier performance, ensures compliance with quality standards, and manages approvals.
- Risk management | Identifies and mitigates risks to product quality and operational efficiency. Includes tools for failure mode and effects analysis (FMEA) and risk assessments.
- Reporting and analytics | Provides insights into quality performance through dashboards and customizable reports and tracks metrics such as defect rates, on-time delivery, and customer satisfaction.
- Does not typically include:
- Single-software application | QMS is a comprehensive framework that may use multiple tools and platforms, rather than a standalone software solution.
- Production management | While QMS ensures quality in production, it doesn’t manage production schedules or inventory.
- Project management | QMS focuses specifically on quality-related activities and metrics, not on managing timelines, budgets, or team tasks unrelated to quality.
What is Radio Frequency Identification (RFID)?
- Abbreviation: RFID = Radio Frequency IDentification (Types: Active, Passive, Semi-Passive)
- RFID Definition: A Radio Frequency Identification (RFID) device is a technology that uses electromagnetic fields to identify and track objects via RFID tags. These tags store data that can be read by an RFID reader, enabling quick and contactless identification and data exchange across various industries, including logistics, retail, healthcare, and agriculture.
- Industry applications: RFID devices are used for efficient identification and tracking, leveraging contactless communication to streamline operations in logistics, healthcare, and retail. While they excel in short-range, high-speed data exchange, RFID is not suitable for applications requiring continuous, wide-range tracking or bi-directional communication. This makes RFID a powerful but specialized tool in the broader ecosystem of tracking and data collection technologies.
- Typical features:
- Physical device | Small, lightweight “tag” devices that store data and can be attached to objects or embedded in items. These are available in active (powered) or passive (powered by the reader’s signal) formats.
- Readers | RFID readers are devices, which can be handheld or fixed, that emit radio waves to communicate with RFID tags, capturing stored information like product IDs or serial numbers.
- Frequency bands | Operates in different frequencies, such as low-frequency (LF), high-frequency (HF), and ultra-high-frequency (UHF), based on use cases and range requirements.
- Unique identification | Each RFID tag contains a unique identifier (UID) for accurate tracking and management of items.
- Data storage on device | Tags can store small amounts of data, such as asset information, timestamps, or batch numbers, depending on their type.
- Contactless communication | Tags are read without direct line-of-sight, enabling scanning through materials like cardboard, plastic, or fabrics.
- Variable range | Supports a variety of ranges, from a few centimeters (e.g., HF tags) to several meters (e.g., UHF tags or active RFID).
- Device durability | RFID tags are designed to withstand harsh environments, including extreme temperatures, moisture, and vibration.
- Rapid scanning | Readers are capable of reading multiple tags simultaneously, enabling faster operations compared to barcode systems.
- Does not typically include:
- Real-time tracking | RFID devices provide location data only within the range of an RFID reader and cannot provide continuous real-time tracking across wide areas.
- High-capacity data storage | RFID tags can store limited data, unlike systems designed for extensive data storage like IoT platforms.
- Wide-range communication | Unlike technologies like LoRaWAN or cellular networks, RFID is limited to short-range communication, even with UHF or active tags.
- Standalone technology | RFID requires integration with readers and software platforms for tracking and analysis; it doesn’t function independently.
- IoT system replacement | RFID tags provide identification and tracking but lack the sensors and advanced communication capabilities of IoT devices.
- Bi-directional communication | RFID primarily supports one-way data transfer from tags to readers, unlike NFC, which allows two-way communication.
- Active tag power | Active RFID tags require a power source, making them different from passive tags powered by the reader.
- Barcode system replacement | While RFID offers more capabilities than barcodes, it is not always suitable due to higher costs or the need for specialized readers.
What is Robotic Process Automation (RPA) System?
- Abbreviation: RPA = Robotic Process Automation
- RPA Definition: A Robotic Process Automation (RPA) system is a software technology that automates repetitive, rule-based tasks by mimicking human interactions with digital systems. RPA systems streamline workflows, reduce manual effort, and improve accuracy in business processes by using software robots or “bots” to handle high-volume, routine tasks across applications.
- Industry applications: RPA’s automate repetitive, rule-based tasks across digital systems to increase efficiency, reduce errors, and free up human resources for higher-value work. While RPA excels in handling structured, predefined processes, it is not a substitute for dynamic decision-making, AI-driven solutions, or physical automation, making it a critical but focused tool for operational efficiency.
- Typical features:
- Task automation | Automates repetitive tasks such as data entry, form filling, file transfers, and report generation. RPAs execute tasks faster and more consistently than humans.
- Screen scraping data capture | Extracts data from digital interfaces, including structured and semi-structured sources like PDFs, emails, and spreadsheets.
- Application integration | Works across multiple applications (e.g., ERP, CRM, legacy systems) without requiring APIs, often interacting through the user interface.
- Rule-based decision making | Automates processes that follow specific, predefined rules, such as invoice matching or email sorting.
- Workflow orchestration | Configures bots to execute sequences of tasks within a broader business process.
- Reporting and analytics | Tracks bot performance, provides logs, and offers insights into process efficiencies and errors.
- Compliance and audit trails | Ensures adherence to regulatory requirements by maintaining detailed records of bot activities.
- Does not typically include:
- Artificial intelligence (AI) | RPAs follow predefined rules and lacks the ability to learn or adapt unless combined with AI technologies like machine learning or natural language processing.
- Dynamic decision making | An RPA cannot handle tasks requiring judgment, creativity, or complex decision-making beyond its programmed rules.
- System development | An RPA interacts with existing systems but does not develop, modify, or enhance underlying software applications.
- Process improvement | An RPA optimizes existing workflows but does not inherently redesign or improve inefficient processes.
- Hardware-based automation | RPA operates entirely in software and does not involve physical robotics or machinery automation.
What is a Real-Time Location System (RTLS)?
- Abbreviation: RTLS = Real-Time Location System
- RTLS Definition: A Real-time Location System (RTLS) is a technology solution designed to continuously identify and track the location of assets, equipment, or people in real time within a defined area, such as a warehouse, hospital, or manufacturing facility. RTLS uses various technologies like GPS, RFID, Bluetooth, Wi-Fi, or Ultra-Wideband (UWB) to deliver accurate location data for operational visibility and efficiency.
- Industry applications: This provides precise, real-time location data to enhance operational efficiency, improve asset visibility, and support location-driven decision-making within defined areas. While RTLS excels in localized, real-time tracking, it is not a substitute for broader tracking technologies like GPS or systems designed for inventory, asset lifecycle, or environmental monitoring, making it a key tool for location-centric industries.
- Typical features:
- Tracking and monitoring | Tracks the precise location of objects, vehicles, or personnel in real time within a defined space.
- Tag and sensor integrations | Devices such as RFID tags, Bluetooth beacons, or UWB tags that attach to assets or personnel for tracking. Offers different levels of accuracy based on technology (e.g., UWB for high precision or Wi-Fi for broader coverage).
- Anchor or reader integrations | Fixed devices like GPS, Bluetooth (or BLE) gateways, or UWB anchors that communicate with tracking tags to determine location.
- Visualization and mapping | Dashboards and maps that display asset or personnel locations in real time for operational visibility.
- Alerts and notifications | Configurable alerts for specific events, such as items leaving a designated area (geofencing) or equipment requiring maintenance.
- Integration with management systems | Links with ERP, WMS (Warehouse Management Systems), or CMMS (Computerized Maintenance Management Systems) for seamless operations.
- Data storage and analytics | Stores historical location data for reporting, analytics, and trend identification.
- Scalable | Supports adding more tracked items, users, or spaces as business needs grow.
- Does not typically include:
- Wide-area tracking | RTLS is typically limited to defined indoor or localized outdoor areas, unless GPS hardware is incorporated as a part of the solution, as GPS allows for tracking across wide geographic regions.
- Standalone asset management | RTLS provides location data but does not typically manage asset lifecycles, inventory, or maintenance unless integrated with other systems.
- Messaging and communication | RTLS specializes in location tracking and doesn’t include broader communication capabilities like messaging or collaboration tools.
- Physical security system | While RTLS can enhance security by tracking assets or people, it doesn’t replace security measures like surveillance cameras or access control.
What is a Returnable Transport Inventory (RTI) System?
- Abbreviation: RTI = Returnable Transport Inventory (i.e. Returnable Containers) System
- RTI Definition: A Returnable Transport Inventory (RTI) system is a solution designed to track, manage, and optimize reusable transport items such as pallets, containers, bins, and racks. These systems ensure that RTIs are efficiently circulated, maintained, and accounted for within supply chains, reducing losses, enhancing visibility, and minimizing costs associated with replacement and inefficiencies.
- Industry applications: While RTI systems excel in tracking and optimizing reusable assets, they are not intended for managing disposable packaging, finished goods inventory, or logistics efficiencies, making them a specialized tool for companies like original equipment manufacturers (OEM’s), construction, manufacturing, agriculture, and other industries using returnable containers and equipment.
- Typical features:
- Tracking and identification | Uses technologies like mesh-networked GPS and BLE to uniquely identify and track RTIs.
- Inventory management | Monitors the current stock of RTIs at various locations, including warehouses, suppliers, and customer sites, and tracks availability and usage to avoid shortages or overstocking.
- Utilization tracking | Records RTI usage patterns to identify inefficiencies, such as underutilization or excessive idle time.
- Return cycle management | Tracks the flow of RTIs through their lifecycle, from dispatch to customer use, return, and maintenance.
- Loss prevention | Monitors RTIs to prevent loss or theft, often with geofencing alerts or location-based data.
- Data integration | Integrates with ERP, supply chain, and warehouse management systems for real-time updates and centralized management.
- Reporting and actionable analytics | Generates insights on RTI utilization, return cycles, and costs to optimize processes and reduce waste.
- Compliance management | Ensures adherence to regulatory requirements for RTIs used in food, pharmaceuticals, or other industries with strict standards.
- Does not typically include:
- Disposable packaging management | RTI systems are specifically designed for reusable transport items and do not manage one-time-use packaging.
- Supply chain planning tools | RTI systems optimize RTI movement and usage but don’t provide overall supply chain planning or forecasting capabilities.
- Inventory management for finished goods | RTI systems manage reusable transport containers, not the products being shipped inside them.
- Standalone condition monitoring | RTI systems don’t monitor conditions like temperature or humidity unless paired with IoT sensors for specific use cases.
- Route planning & optimization | RTI systems are a specialized subset of logistics tools focusing on returnable assets, not broader transportation or route optimization.
What is a Supply Chain Management (SCM) System?
- Abbreviation: SCM = Supply Chain Management (System)
- SCM Definition: A Supply Chain Management (SCM) system is a platform or software solution designed to manage and optimize the end-to-end flow of goods, information, and finances across the supply chain, from raw material procurement to final product delivery. SCM systems aim to enhance efficiency, reduce costs, and ensure the timely delivery of products by providing visibility and control over supply chain processes.
- Industry applications: While SCM systems encompass logistics, procurement, and inventory management, they do not handle unrelated processes like employee management, product design, or facility maintenance, making them a comprehensive but focused tool for supply chain operations.
- Typical features:
- Procurement management | Facilitates sourcing and purchasing of raw materials, components, or goods from suppliers as well as tracking purchase orders, supplier performance, and contract compliance.
- Inventory management | Monitors inventory levels across warehouses, distribution centers, and retail locations. Provides demand forecasting to optimize stock levels and prevent overstocking or shortages.
- Warehouse management | Manages storage, organization, picking, packing, and shipping of goods within warehouses. Optimizes space utilization and workflow efficiency.
- Transportation management | Plans and monitors the movement of goods, including route optimization, freight scheduling, and tracking. Manages multiple transportation modes (e.g., truck, rail, air, sea).
- Order fulfillment | Oversees the process of receiving, processing, and delivering customer orders, ensuring accurate and timely fulfillment.
- IoT integration | Integrations with hardware provides real-time tracking of goods and materials throughout the supply chain. Frequently leverages data from IoT devices, GPS, and BLE for enhanced transparency.
- Demand planning and forecasting | Helps optimize production and inventory levels by analyzing historical sales data, market trends, and external factors to predict future demand.
- Risk management and compliance | Identifies and mitigates supply chain risks, such as disruptions or compliance violations; it also ensures adherence to industry standards and regulatory requirements.
- Does not typically include:
- Production planning tools | SCM focuses on the broader supply chain, while specific production scheduling and manufacturing workflows are often handled by MES (Manufacturing Execution Systems).
- Product lifecycle management (PLM) | SCM systems track goods through the supply chain but don’t manage the design or development phases of products.
- Facility management | These systems don’t handle the physical maintenance or utilities of warehouses and facilities.
What is a Transportation Management System (TMS)?
- Abbreviation: TMS = Transportation Management System
- TMS Definition: A Transportation Management System (TMS) is a software platform designed to optimize the planning, execution, and tracking of transportation and logistics operations. TMS solutions help businesses manage shipping, freight, and carrier operations to improve efficiency, reduce costs, and ensure timely delivery of goods.
- Industry applications: A TMS focuses on the efficient movement of goods, providing tools for route planning, carrier management, shipment tracking, and freight cost optimization, making it ideal for procurement and logistics teams across a variety of industries. While TMS integrates with broader supply chain systems, it doesn’t handle inventory, production, or facility management, making it a specialized tool for transportation and logistics operations.
- Typical features:
- Freight planning and optimization | Supports route optimization to minimize distance, costs, or delivery time. A TMS helps select the most suitable transportation mode (e.g., truck, rail, air, sea) and carrier based on requirements.
- Carrier management | Manages relationships with carriers, including contract negotiation and performance monitoring and provides tools to evaluate each carrier based on cost, delivery time, and service quality.
- Shipment booking and scheduling | Automates the scheduling of shipments with carriers by tracking available capacity to maximize efficiency.
- Freight cost management | Tracks freight costs and generates cost comparisons for different carriers or routes and manages invoicing, payment reconciliation, and freight billing auditing.
- Order management | Links with order management systems to ensure accurate and timely shipment fulfillment. Provides updates on shipment status to customers or stakeholders.
- Load consolidation | Combines shipments or freight loads to reduce transportation costs and maximize vehicle utilization.
- Standard shipment reporting | Generates insights into transportation performance, costs, and bottlenecks through dashboards and reports.
- Regulatory compliance | Ensures adherence to regulations like HOS (Hours of Service), customs requirements, and hazardous material handling.
- Does not typically include:
- Real-time tracking | While many TMS platforms suggest they offer real-time visibility, this is something to check into. What many carriers call “real-time visibility” often consists of tracking using check-points. Estimated times of arrival (ETAs) are calculated based on these check-points or scans.
- Inventory management | Does not track stock levels, warehouse organization, or inventory forecasting.
- Supply chain management (SCM) | A TMS doesn’t encompass the broader functions like procurement, manufacturing, or supplier management.
- Fleet maintenance | Vehicle maintenance schedules or repair management are managed by CMMS or fleet management systems.
- Production planning | Manufacturing workflows or production schedules are handled by MES (Manufacturing Execution Systems).
- eCommerce order processing | A TMS may integrate with e-commerce platforms for shipment execution but doesn’t process online orders directly.
What is an Ultra-High Frequency (UHF) device?
- Abbreviation: UHF = Ultra-High Frequency
- UHF Definition: An Ultra-High Frequency (UHF) device operates within the radio frequency range of 300 MHz to 3 GHz and is commonly used for communication, tracking, and data transmission. UHF technology is widely utilized in RFID systems, telecommunications, and broadcasting due to its ability to cover long distances and penetrate obstacles better than higher frequencies.
- Industry applications: UHF is a versatile tool for medium-to-long-range communication, particularly in RFID applications for asset tracking, inventory management, and logistics. While UHF excels in efficient, scalable data transmission for identification and tracking, it does not provide continuous location updates, high data throughput, or the broader capabilities of IoT (like GPS) systems. This makes it a specialized but powerful technology for industries requiring reliable, fast, and cost-effective solutions.
- Typical features:
- Broad communication range | Supports communication over long distances, ranging from several meters to tens of kilometers, depending on the device and environment.
- RFID integration | UHF is commonly used in RFID tags and readers, enabling quick identification and tracking of items or assets.
- Low power consumption | Optimized for energy-efficient operation, especially in passive UHF RFID tags that derive power from the reader’s signal.
- Data transmission | Capable of transmitting small amounts of data, such as identification codes or sensor readings, efficiently over the UHF band.
- Penetration through obstacles | Can pass through non-metallic materials like plastics, wood, and cardboard, making it suitable for applications like inventory tracking.
- High-speed reading | UHF RFID readers can scan numerous tags quickly, enabling fast processing in high-throughput environments.
- Durable tag options | UHF tags are available in robust formats that can withstand harsh environmental conditions, including extreme temperatures or exposure to chemicals.
- Does not typically include:
- Short-range communications | Unlike technologies like NFC or low-frequency RFID, UHF is optimized for medium to long-range communication and is not typically used for ultra-close proximity applications.
- Continuous or real-time location | UHF RFID provides location data only when tags are within range of a reader, unlike GPS or RTLS systems, which provide continuous real-time tracking.
- Data-intensive communication | UHF devices are not designed for high-bandwidth data transmission, such as streaming video or large file transfers.
- Standalone systems | UHF devices require complementary hardware (like readers and gateways) and software to capture, process, and analyze data.
- Unrestricted obstacle penetration | While UHF can penetrate many materials, it is less effective with metal or liquids, which can interfere with signal strength.
- Power-reliance for active tags | Passive UHF tags rely on reader signals for power and don’t operate independently; tags actively tracking require a power source for extended functionality.
- Condition monitoring | UHF doesn’t inherently include advanced IoT capabilities like condition monitoring or predictive analytics.
What is Ultra-Wide Band (UWB)?
- Abbreviation: UWB = Ultra-Wide Band
- UWB Definition: An Ultra-Wideband (UWB) device uses radio waves over a wide frequency spectrum (typically 3.1 to 10.6 GHz) to provide highly accurate and low-latency location tracking, communication, and data transfer. UWB technology is widely used in real-time location systems (RTLS), indoor navigation, and proximity-based applications due to its precision and ability to operate in cluttered environments.
- Industry applications: This technology offers high-precision, low-latency location tracking and communication within short to medium ranges, making it a powerful tool for applications like RTLS, proximity sensing, and indoor navigation. While UWB excels in accuracy and responsiveness, it is not designed for long-range tracking, high-bandwidth communication, or cost-sensitive scenarios, making it best suited for specialized use cases in industries that prioritize precision and real-time data.
- Typical features:
- High precision location tracking | Provides centimeter-level accuracy for real-time positioning, making it ideal for RTLS in indoor environments.
- Wide frequency range | Operates across a broad spectrum of frequencies, reducing interference and enabling reliable communication in dense environments.
- Low latency | Delivers near-instantaneous data transmission, ensuring responsiveness for applications like collision avoidance or proximity sensing.
- Multipath resistance | Effectively handles signal reflections, making it suitable for complex environments like warehouses, factories, or hospitals.
- Low power consumption | Optimized for energy efficiency, enabling long battery life for devices like asset tags or wearable sensors.
- High data transfer rate | Supports fast data exchange for short-range applications, though typically less than other high-speed technologies like Wi-Fi.
- Secure communication | Offers inherent security due to its short range, precision, and difficulty in intercepting UWB signals.
- Scalable | Capable of managing multiple devices or tags simultaneously, making it ideal for large-scale operations.
- Does not typically include:
- Long-range tracking | Optimized for short to medium-range applications (typically under 100 meters) and is not suited for wide-area tracking like GPS.
- High-bandwidth applications | UWB is not designed for high-bandwidth tasks like video streaming or large data transfers over extended distances.
- Stand-alone systems | Devices require anchors, tags, or receivers and are not independent tracking solutions without supporting infrastructure.
- Interference-restricted | May not be ideal for outdoor or high-interference environments like metal-heavy locations.
- Low-cost hardware | Hardware is often more expensive than simpler tracking technologies like Bluetooth, making it less ideal for basic use cases.
What is Wide Area Networking (WAN)?
- Abbreviation: WAN = Wide Area Networking
- WAN Definition: Wide Area Networking (WAN) technology connects multiple local area networks (LANs) or devices across broad geographic areas, enabling communication and resource sharing over distances that range from city-wide to global. WANs are typically used by businesses, governments, and organizations to support large-scale networking needs, such as connecting branch offices or enabling access to centralized resources.
- Notable: Software-defined WAN (SD-WAN) is a more modern WAN technology, which uses software to optimize traffic routing, improve performance, and reduce costs.
- Industry applications: WANs are often a critical backbone for modern global enterprises and organizations, as they’re able to bridge long distances and support large-scale operations.
- Typical features:
- Geographic coverage | Extends connectivity over wide areas, such as between cities, countries, or continents.
- Network infrastructure | Utilizes leased lines, satellite links, fiber optics, cellular networks, or the public internet for connectivity.
- Centralized management | Offers tools for monitoring, configuring, and managing network traffic and performance across all connected sites.
- Data transmission | Facilitates the transfer of files, emails, application data, and other communications between distant locations.
- Security | Implements firewalls, intrusion detection systems, and encryption to protect data during transmission.
- Either wired or wireless | WANs can include both wired (fiber, MPLS) and wireless (satellite, 4G/5G) technologies.
- Does not typically include:
- Local networking (LAN) | Unlike LANs, which are confined to a single building or campus, WANs operate over much larger distances.
- Not application-specific | WANs are general-purpose networks designed for a wide range of data types and use cases, unlike IoT-specific or industrial networks.
- High-speed | While WANs can achieve high speeds, they are generally slower than LANs due to greater distances and potential congestion.
- Cloud services | While WANs connect locations, they do not provide storage, computing, or application hosting like cloud platforms.
What is a Warehouse Management System (WMS)?
- Abbreviation: WMS = Warehouse Management System
- WMS Definition: A Warehouse Management System (WMS) is a software solution designed to manage, control, and optimize warehouse operations and inventory storage. WMS solutions ensure efficient workflows, accurate inventory tracking, and streamlined order fulfillment processes, helping businesses maintain high productivity and customer satisfaction.
- Industry applications: WMS tools are a critical but focused component of logistics and inventory management strategies, as they enhance operational efficiency within warehouse facilities.
- Typical features:
- Inventory tracking and management | Provides real-time visibility of inventory levels, locations, and movements within the warehouse, often able to track across multiple warehouses or storage facilities.
- Order fulfillment | Coordinates picking, packing, and shipping workflows to ensure accurate and timely order fulfillment.
- Receiving & returns management| Manages incoming shipments, including inspection, labeling, and assigning storage locations. Handles reverse logistics by managing returned goods, inspection, and restocking or disposal.
- Space optimization and “slotting” | Analyzes product dimensions, demand, and movement to determine the best storage locations.
- IoT integration | Supports technologies that track inventory movements and reduce errors in manual processes.
- Labor management | Tracks employee productivity and task assignments to optimize workforce efficiency.
- Reporting and analytics | Offers dashboards and reports on key performance indicators (KPIs), such as order accuracy, picking speed, and inventory turnover.
- Does not typically include:
- Broader supply chain management | Does not handle broader supply chain processes like procurement or transportation.
- Manufacturing execution | A WMS doesn’t manage production workflows or shop-floor operations, which are handled by MES solutions.
- Facility management | These tools do not manage physical warehouse maintenance or utilities.
- Financial management | WMS’ do not handle accounting, invoicing, or financial reporting, though it may provide cost metrics related to inventory and labor.
Want to learn more about how GPX Intelligence can help you navigate the alphabet soup of supply chain tech? Contact us.
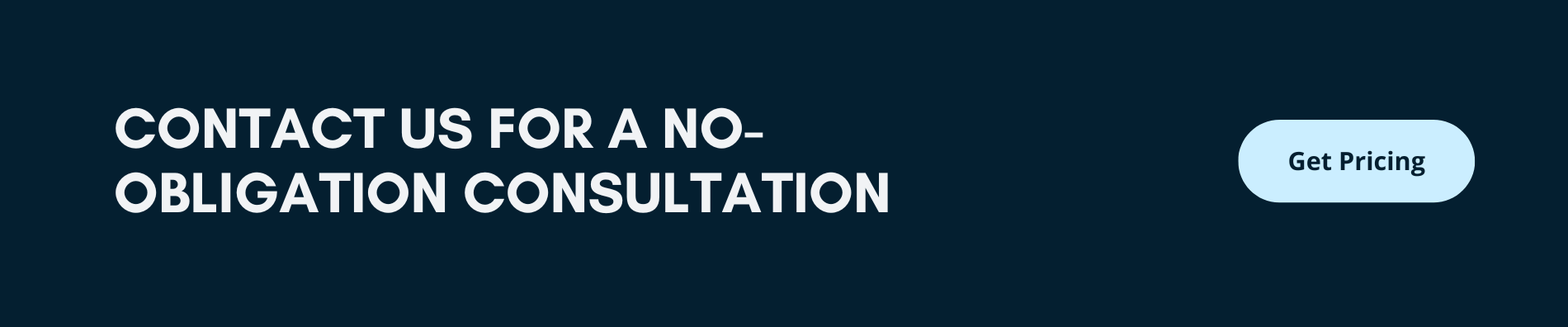